TIG溶接とは?様々な種類や特徴、基礎知識を解説!
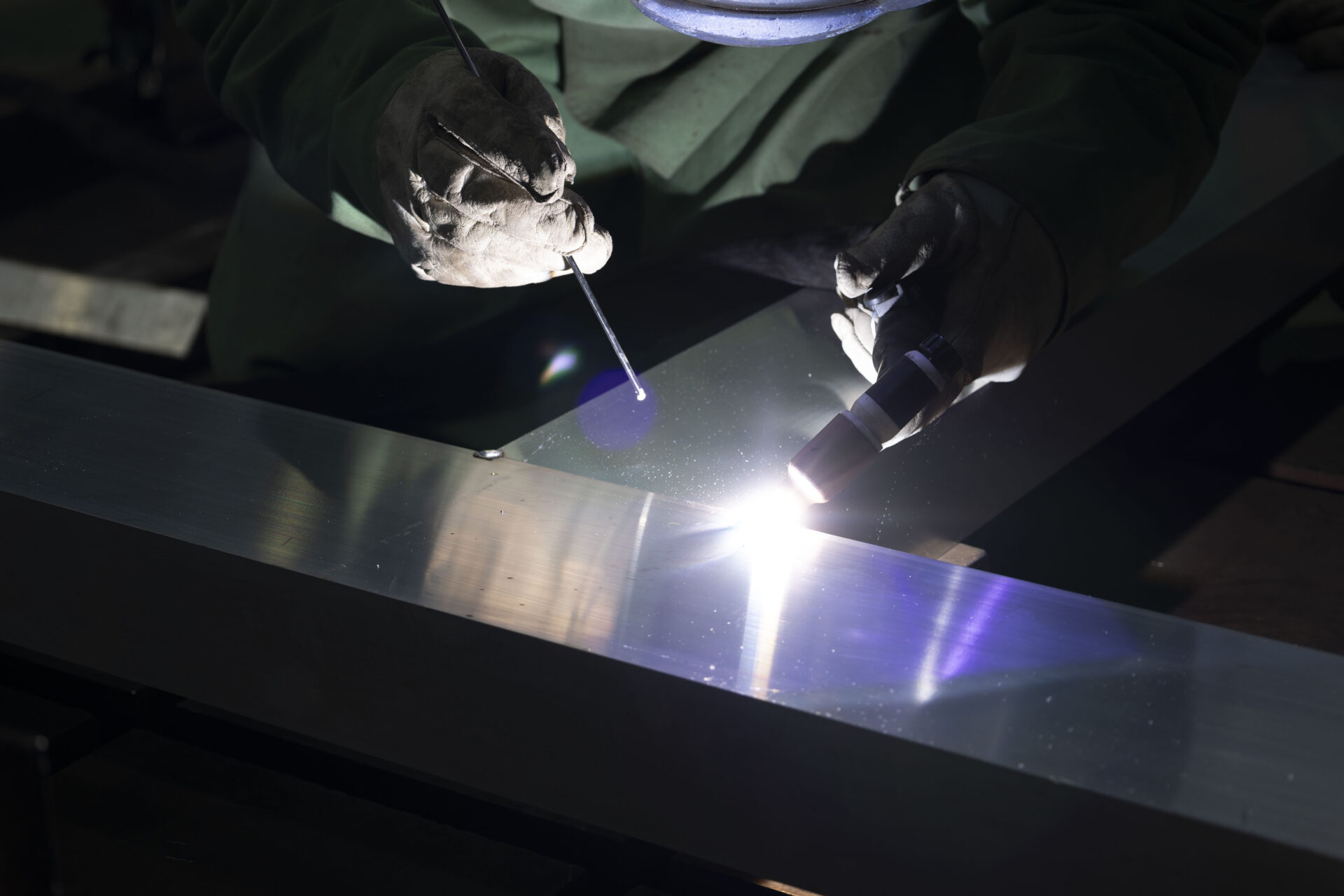
TIG溶接は、さまざまな金属材料に対して高品質な溶接を可能にするため、多くの製造業で利用されている溶接法です。特に、鉄鋼やステンレスだけでなく、アルミニウムの溶接にも適しており、幅広い用途で重宝されています。しかし、TIG溶接には直流、交流、パルス、高速といった複数の種類があり、それぞれの特性と適用方法が異なるため、目的に合わせて最適な手法を選定することが重要です。この記事では、各TIG溶接の種類とその特徴を詳しく解説し、さらにアルミ溶接におけるTIG溶接の利点や課題についても紹介していきます。
TIG溶接とは? 基礎知識
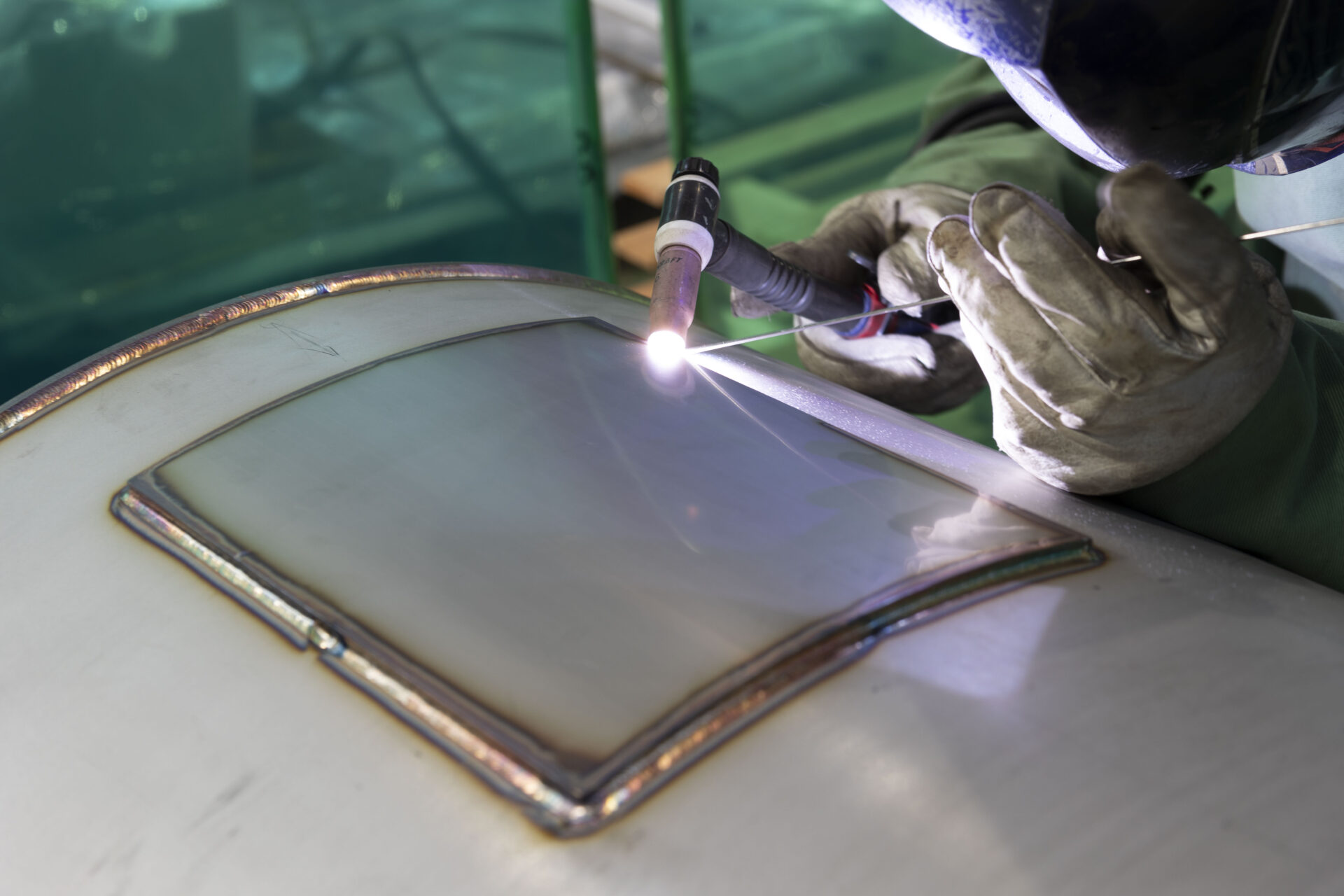
TIG(ティグ)溶接は、高品質な仕上がりと優れた耐久性を実現できる溶接法として、さまざまな産業で採用されています。この溶接法は、タングステン電極とシールドガス(主にアルゴンやヘリウム)を用いてアークを発生させ、安定した熱源を利用して接合部を溶接します。特に、熱伝導率が高く、熱管理が難しいアルミニウムやチタンなどの材料にも適しているため、航空機部品や医療機器の製造など、高い精度を求められる場面で活用されています。
ここでは、TIG溶接の基本知識や仕組みについて詳しく解説します。
TIG溶接の仕組み
TIG(ティグ)溶接は、アーク溶接の一種で、融点の高いタングステン電極を用いて金属を接合する手法です。溶接中、電極自体は溶融せず、アークを安定させる役割を果たし、溶接部の酸化を防ぐためにシールドガスとしてアルゴンやヘリウムなどの不活性ガスを使用します。これにより、スパッタ(溶接時の飛び散り)をほとんど発生させず、仕上がりが美しいのが特長です。
TIG溶接は、火花が散らないため製品の表面を美しい状態に保つことができ、航空宇宙分野や精密機器の製作など、特に高い品質が求められる場面で使用されます。また、タングステン電極とシールドガスを活用することで、アルミやステンレスなど多様な金属を接合でき、熱伝導性や溶け込み性にも優れた溶接が可能です。
TIG溶接は熟練した技術者による手動作業が多く、その分制御が難しいため、溶接品質を維持するには高度な技術と経験が必要とされます。しかし、その分、精度の高い接合と美しい仕上がりが得られることから、高性能・高品質な溶接方法として広く評価されています。
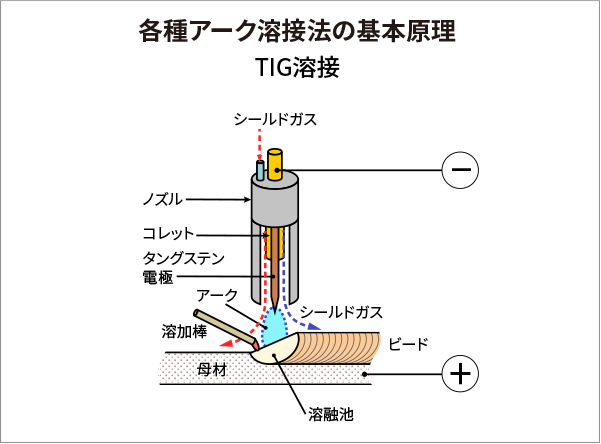
TIG溶接が適している材料
TIG溶接は、ステンレス鋼やアルミニウム合金、チタン、銅、マグネシウム合金など、多くの金属材料に適用できる溶接方法です。タングステン電極と不活性ガスを使用することで、金属が酸素や窒素などの影響を受けにくく、安定した品質の溶接が可能になります。
特に、酸化しやすいアルミニウム合金やマグネシウム合金は、溶接中に酸化被膜が発生しやすく、品質を損なうリスクがありますが、TIG溶接ではアルゴンやヘリウムといった不活性ガスを使うことで、酸化被膜を防ぎながら作業ができます。
また、薄板や小さな部品の接合にも適しており、熱の制御が容易なため、熱歪みを抑えた精密な溶接を実現できます。そのため、航空機、自動車、医療機器などの産業分野で広く採用されています。
TIG溶接の種類と特徴
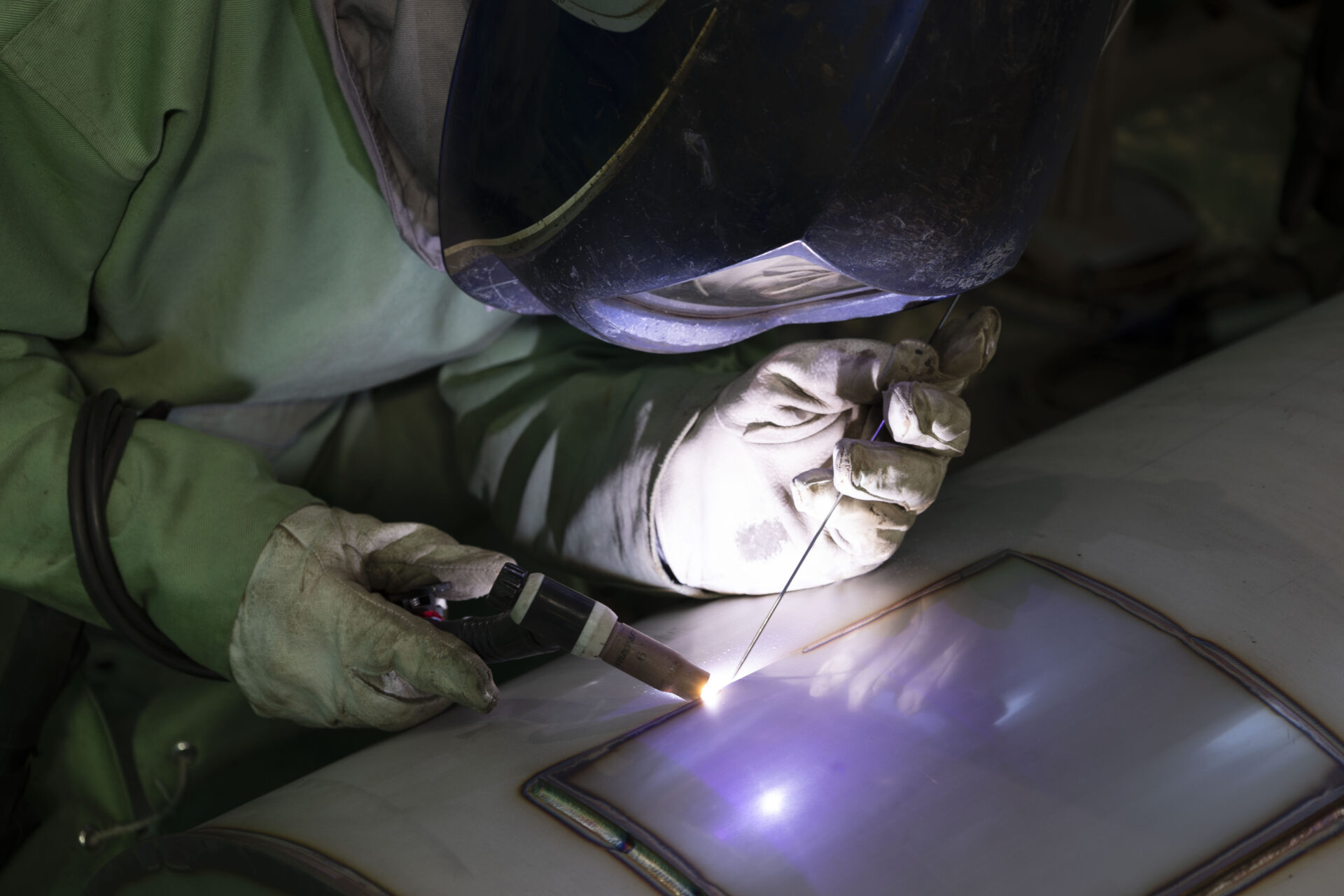
TIG溶接にはさまざまな種類が存在し、それぞれの特性や用途に応じて選定されます。例えば、直流(DC)TIG溶接は鉄鋼やステンレス鋼の溶接に適し、交流(AC)TIG溶接はアルミニウムやマグネシウムの溶接に最適です。さらに、パルスTIG溶接や高速TIG溶接といった特殊な溶接方法も存在し、精密な仕上がりや高速な溶接を実現できます。
ここでは、各TIG溶接の種類とその特徴について詳しく解説していきます。
1.直流(DC)TIG溶接
直流(DC)TIG溶接は、溶接時に常に一定方向に電流を流すことで、安定したアークを形成し、母材の深部まで溶け込むことを可能にする溶接方式です。この仕組みでは、溶接電極(タングステン)が負極、母材が正極に設定され、電流が母材側に集中します。これにより、熱が効率的に伝達され、厚みのある鋼材やステンレス鋼の溶接に適しています。
直流TIG溶接の最大の特徴は、アークの安定性と高い制御性です。アークが安定しているため、溶接ビードの形成が均一で、精度の高い仕上がりが得られます。また、操作性が良いため、熟練度に関係なく精密な溶接を行いやすいのも利点です。
さらに、直流TIG溶接は他の溶接法と比較して深い溶け込みを得られるため、溶接部の強度も高く、溶接後の強度や耐久性が重要視される構造物の溶接に広く用いられます。ただし、アルミニウムやマグネシウムなどの酸化しやすい金属の溶接には不向きであり、これらの材料を溶接する際には、交流(AC)TIG溶接が適しています。
このように、直流TIG溶接は特定の用途や材質に適しており、溶接部の品質を確保しつつ、作業を安定させることが可能です。
2.交流(AC)TIG溶接
交流(AC)TIG溶接は、アルミニウムやマグネシウムなどの非鉄金属の溶接に適した溶接方法です。直流(DC)TIG溶接とは異なり、交流電流を用いることで、溶接電極の極性がプラスとマイナスに交互に切り替わる特性を持ちます。この極性の切り替えによって、溶接中に発生する酸化被膜を効率的に除去し、母材表面をクリーンな状態に保つことができます。
具体的には、交流TIG溶接のプラス極のときには母材表面に蓄積された酸化被膜を除去し、マイナス極のときには熱が深く母材に浸透し、しっかりとした溶け込みを実現します。これにより、アルミニウムなどの酸化被膜を持つ金属を効率よく溶接することができ、溶接品質が向上します。
また、交流TIG溶接はアークの安定性が高く、均一で滑らかなビードを形成することができるため、美しい仕上がりを求める用途にも適しています。ただし、交流電流を用いるため、直流TIG溶接に比べて電力消費が多く、また電極の消耗も激しくなる点がデメリットとして挙げられます。
このように、交流TIG溶接は非鉄金属の溶接において優れた性能を発揮し、酸化被膜の除去と深い溶け込みの両立を可能にする溶接法です。
3.パルスTIG溶接
パルスTIG溶接は、溶接電流をパルス状(一定の周波数でオンとオフを繰り返す)にすることで、アークの安定性と溶接の制御性を向上させた溶接方法です。パルスTIG溶接では、ベース電流とピーク電流の2つの異なる電流値を交互に流すことによって、熱量を効率的に調整できるため、熱影響を抑えた精密な溶接が可能です。
具体的には、ピーク電流時にはアークが強くなり、溶接部の溶け込みが促進される一方、ベース電流時には熱量が抑えられ、アークの安定性が保たれます。この仕組みにより、薄板の溶接や熱変形を抑えたい場合に非常に効果的です。
パルスTIG溶接の最大のメリットは、熱による影響を最小限にしながら精度の高い溶接ができる点です。これにより、ステンレスやアルミニウムなどの熱変形しやすい材料の溶接において、歪みを抑えながら高品質な仕上がりを実現できます。また、パルス周波数や電流の設定を変えることで、溶接速度や溶け込みの深さを柔軟に調整できるため、さまざまな条件に対応可能です。
ただし、パルスTIG溶接は設定の調整が複雑であり、熟練した技術者が適切なパラメータを設定する必要があるため、高い技術力が求められる点に注意が必要です。
4.高速TIG溶接
高速TIG溶接は、その名の通り、従来のTIG溶接に比べて高い溶接速度を実現する溶接法です。この溶接法は、アークの熱源を制御しながら、短時間で溶接を完了するため、作業効率の向上やコスト削減に貢献します。高速TIG溶接では、アークの集束性を高めることで熱の集中度を上げ、溶接部に対する熱の影響を最小限に抑えつつ、溶け込みの深さを確保することが可能です。
具体的には、アークの安定性を保ちつつ高出力の電流を短時間で流すことで、溶接速度を上げながらも均一で精度の高い溶接を実現します。このため、高速TIG溶接は、大型構造物や連続的な溶接作業に適しており、特に製造ラインなどの量産工程において活用されています。
さらに、高速TIG溶接は、溶接速度が速いため、溶接部の熱歪みや変形を抑え、製品の品質を向上させることができます。ただし、設定が複雑で、溶接条件の調整には高度な技術と知識が必要となるため、熟練した技術者の管理のもとで行われることが求められます。
このように、高速TIG溶接は、スピードと品質の両立を図るために開発された高度な溶接法であり、生産性の向上と精度の高い仕上がりを実現する点で優れた特徴を持っています。
TIG溶接のメリット・デメリット
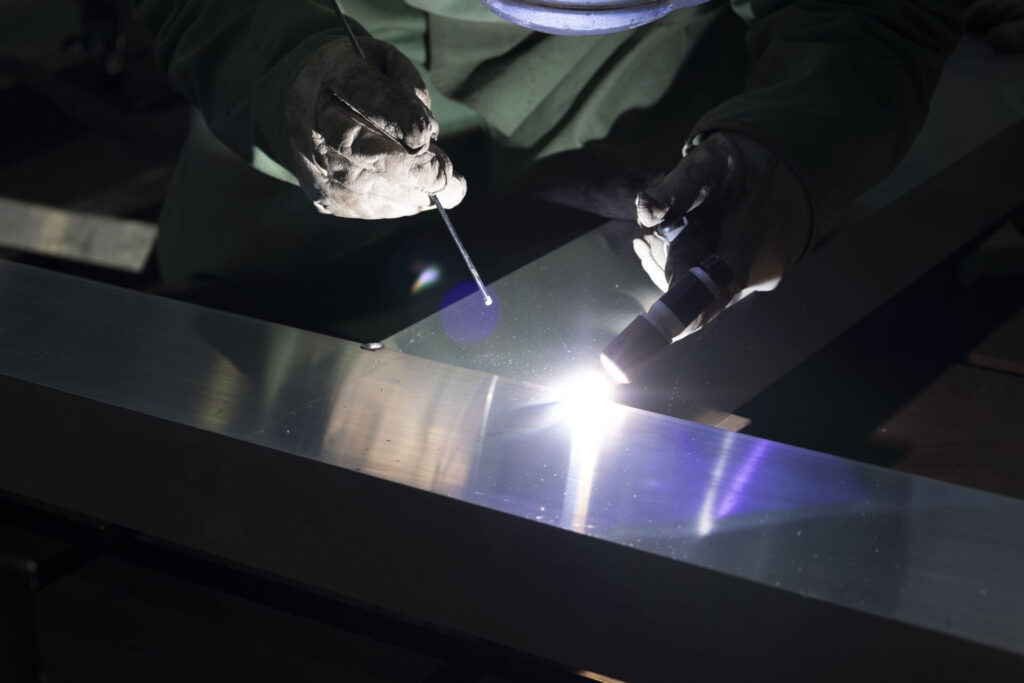
TIG溶接は、他の溶接方法と比較して多くの利点を持っていますが、同時にいくつかの欠点も伴います。精密で美しい仕上がりを実現できる点や、鉄鋼やアルミニウムなど様々な金属に対応できることが大きな特徴です。そのため、航空機や自動車産業など高い品質が求められる分野で広く活用されています。しかし、溶接作業には高度な技術と熟練したスキルが必要で、作業時間が長くなることや生産性が低くなりやすいというデメリットもあります。ここでは、TIG溶接の主なメリットとデメリットについて詳しく解説します。
TIG溶接のメリット
- 高品質な仕上がり
TIG溶接は精度が高く、特に美しいビード(溶接部分の形状)を得られる点が大きな特徴です。シールドガスを使用することで酸化を抑え、非常に美麗な仕上がりが実現できます。そのため、外観品質が求められる製品や繊細な部品の溶接に適しており、装飾品や航空機部品などの製造に多用されます。
- 幅広い材料に対応
鉄鋼やステンレス、アルミニウム、銅、マグネシウムなど、さまざまな材料の溶接が可能です。特に、アルミやステンレスの溶接には最適な手法とされ、精度が求められる電子機器部品や、耐食性が必要な化学プラント設備などに柔軟に対応できます。
- 制御性と安定性が高い
溶接電流やシールドガスの流量を細かく調整できるため、熱の入り方や溶け込み具合をコントロールしやすいです。これにより、熱変形を抑えたい薄板の溶接や、歪みを防ぎたい精密な溶接に最適です。
- スパッタ(溶接時の飛散物)が少ない
他のアーク溶接と比べてスパッタが少なく、仕上がりがきれいで、後処理の手間も軽減されます。鉄鋼やステンレス、アルミなどの材料を溶接する際、スパッタによる表面の粗さや凹凸を抑えられるため、仕上がりの美しさが求められる用途に適しています。
TIG溶接のデメリット
- 溶接速度が遅い
TIG溶接は手動で溶加材を供給しながら行うため、他のアーク溶接法に比べて速度が遅く、生産性がやや劣ります。大規模な構造物や長距離の溶接には不向きで、溶接の進捗速度を優先する場合は、他の溶接法を選ぶことが多いです。
- 熟練技術が必要
TIG溶接は熱や電流の制御が難しく、熟練の技術者でなければ高品質な溶接を安定して行うのが難しいです。特にアルミなどの熱伝導性が高い材料を溶接する際には、熱の管理が重要で、適切な溶接条件を維持するには豊富な経験が必要です。
- コストが高い
TIG溶接は使用する機材やシールドガス、溶加材などの材料が高価で、他の溶接法と比べて初期投資が大きくなります。さらに、使用されるシールドガスや機器のランニングコストも高いため、品質とコストのバランスを考慮する必要があります。
- 作業効率が低下することがある
狭いスペースや複雑な形状のワークピースを溶接する際には、作業効率が低下することがあります。こうした作業では、特別な治具や補助装置の使用を検討し、治具の製作や設置にかかる時間やコストが増加することも少なくありません。
TIG溶接は、その高品質な仕上がりと幅広い対応材料の特徴から、さまざまな産業で利用されています。しかし、溶接速度の遅さや熟練技術の必要性、コストの高さといった課題も伴います。品質を重視したい製品や精密な溶接を必要とする場合に最適な方法ですが、用途や条件に応じて適切な溶接法を選定することが求められます。
アルミ溶接の難易度が高い理由
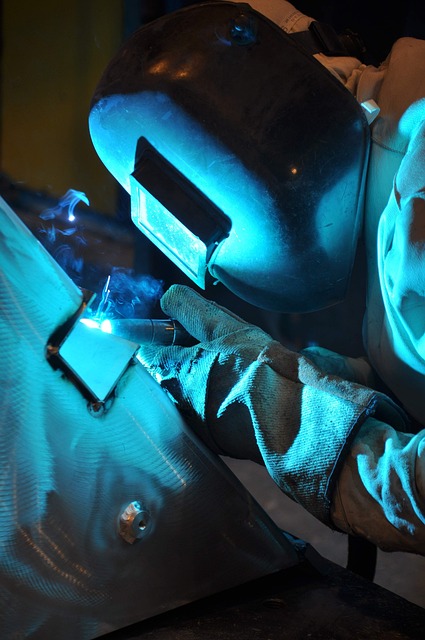
アルミ溶接は、溶接技術の中でも特に高い難易度を要する分野です。その主な理由は、アルミニウムの持つ特性にあります。アルミは他の金属と比べて熱伝導率が非常に高く、溶接時に熱が急速に広がるため、局所的な温度制御が難しくなります。また、酸化被膜が表面に形成されやすく、これが溶接品質に大きく影響を与えることから、溶接者には高度な技術と細かな管理が求められます。
ここでは、アルミ溶接が難しいとされる理由を詳しく解説していきます。
アルミ溶接の難易度が高い理由
アルミニウムの溶接が難しい理由は、熱伝導率の高さと酸化被膜の形成にあります。アルミニウムは鉄やステンレスに比べて熱伝導率が約3倍以上高いため、溶接時に熱が広範囲に拡散しやすく、溶接部分とその周囲の温度管理が困難です。その結果、適切な温度での作業が難しくなり、溶融温度に達するまでの時間が長くなる傾向があります。
さらに、アルミニウムは空気中で酸化被膜を形成しやすく、この被膜が溶接中に溶接部分に混入することで接合不良や内部欠陥の原因となります。そのため、酸化被膜の除去や溶接中のガスシールド管理が重要となります。
TIG溶接がアルミ溶接に向いている理由
TIG溶接は、アルミニウム溶接に特に向いている技術です。主な理由として、温度管理のしやすさ、酸化被膜の除去、そして高いシールド効果が挙げられます。アルミニウムは熱伝導率が高く、溶接時に熱が急速に広がるため、熱制御が難しい素材です。しかし、TIG溶接は熱量を精密に調整できるため、均一な溶接を行いやすく、熱歪みを最小限に抑えることができます。また、交流TIG溶接を用いることで、酸化被膜を除去しながら作業を進めることができ、接合不良を防ぎます。不活性ガスの使用により、溶接中に酸素や水分と接触するのを防ぎ、欠陥の発生を抑えることも可能です。このように、TIG溶接はアルミニウムのような扱いの難しい素材に対しても、品質の高い仕上がりを実現するための適切な技術といえます。
アルミ溶接における熱歪みとその防止技術
アルミニウムは熱伝導率が高いため、溶接中に急激な熱の広がりによって熱歪みが発生しやすい素材です。熱歪みとは、溶接の際に局所的な加熱と冷却が繰り返されることで、金属の形状や寸法が変わる現象を指し、溶接後の製品精度や外観に大きく影響を及ぼします。この歪みを防ぐためには、溶接の順序や位置を工夫して熱の集中を避けることが重要です。さらに、溶接時の熱入力を最小限に抑えるために、溶接速度を上げたり、連続的な溶接ではなく断続的に行う方法(ステッチ溶接)を採用することも効果的です。また、治具を用いて溶接部を固定し、変形を防ぐことも有効な手法です。こうした対策を講じることで、歪みの少ない高品質なアルミ溶接が可能となります。
当社では、アルミニウムの溶接時に発生しやすい熱歪みや変形を最小限に抑えるため、精密な熱管理と溶接技術を組み合わせ、安定した高精度の溶接を実現しています。特に、アルミニウム特有の熱伝導の高さや酸化被膜に対応するため、適切な溶接条件を設定し、独自の工法で熱影響を抑制しています。また、熟練の技術者による溶接工程の管理と、溶接後の品質検査を徹底し、信頼性の高い製品を提供しています。
当社のTIG溶接加工事例
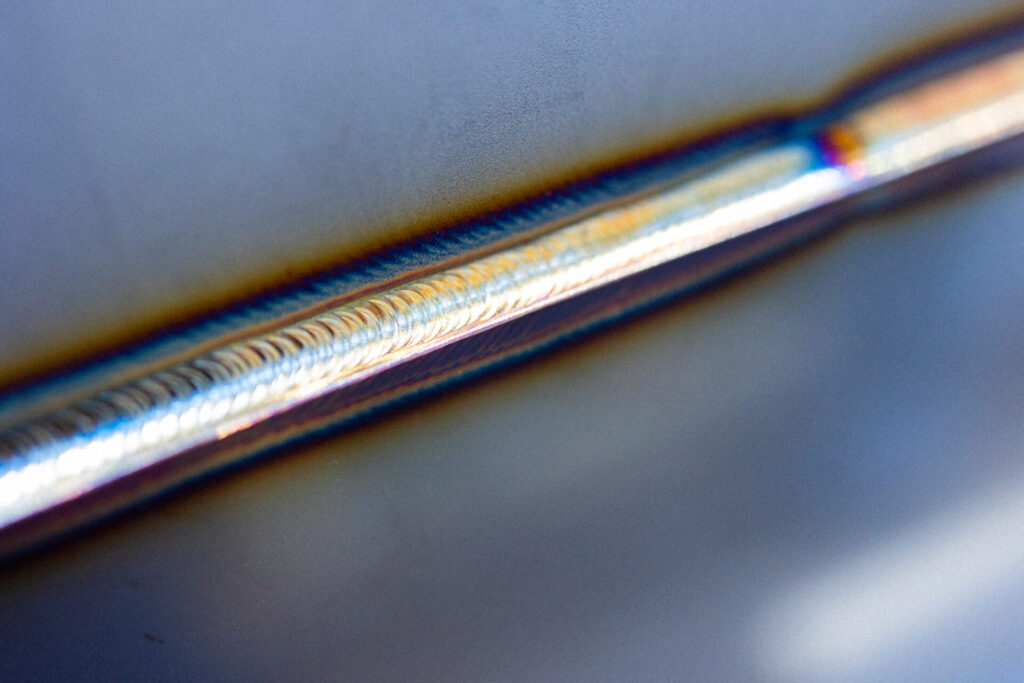
当社では、多種多様なプロジェクトで培った豊富なノウハウと、熟練の技術と高い専門知識を基に、様々な配管溶接や機器の製作に対応しております。高品質・高精度な技術が求められるアルミやステンレスの溶接では、経験豊富な技術者がその技術力を駆使し、お客様のご要望に応えてまいりました。以下に、当社がこれまで手掛けてきた代表的なTIG溶接加工事例をご紹介いたします。どうぞご参考ください。
- 発電プラント内 大径管(SUS200A SCH120)溶接
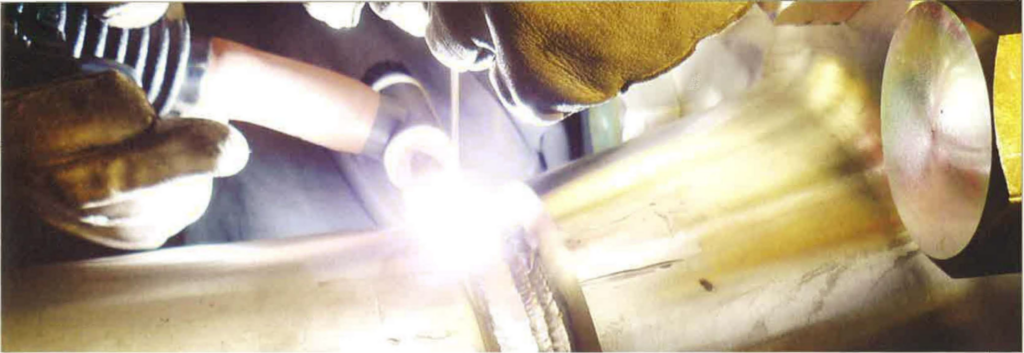
発電プラント内で利用する材質:SUS200A、厚さ:SCH120の大径管の溶接作業です。
高い技術を求められるステンレスかつ厚みを持つ材質なため、歪みを抑えるための予熱や後熱の考慮や
溶接材の選定など、弊社の強みである豊富なノウハウを活かした製品です。
材質 | SUS200A |
厚さ | SCH120 |
開発期間・納期目安 | - |
交差レベル | - |
製品用途 | 発電プラント |
- 発電プラント内 SUS大径管
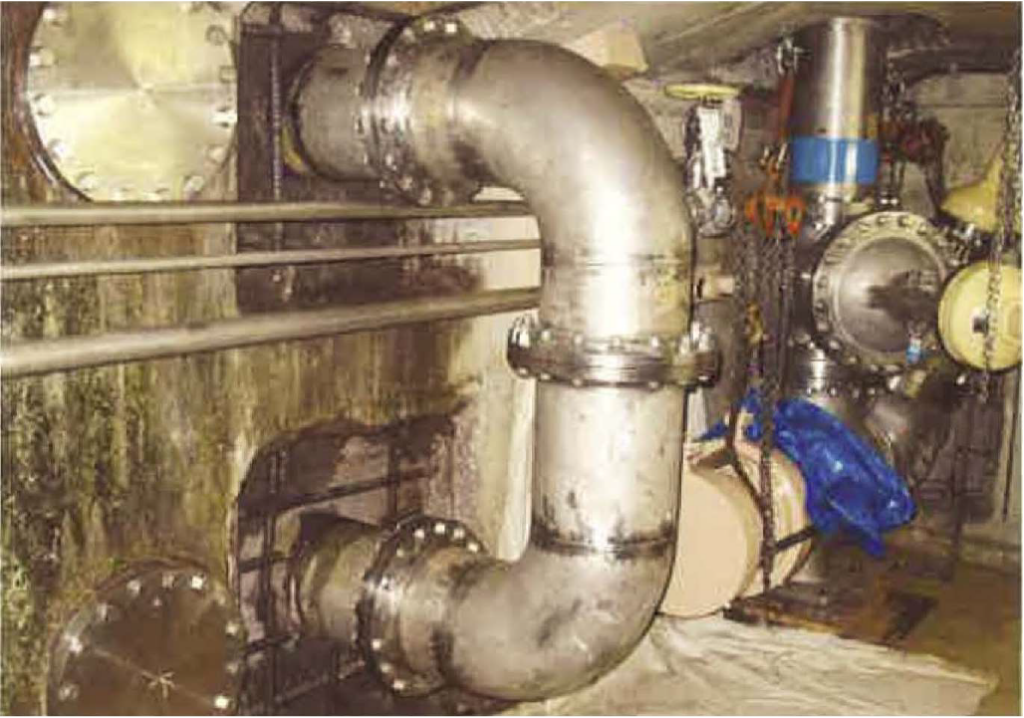
本製品は発電プラントにおけるSUSの大径管です。
ご要望に合わせた部材の製造から、現地の据え付け工事まで一貫にて対応しました。
大物品の取り付け工事となり、信頼性を担保する高い溶接技術が求められますが、弊社の強みであるプラント配管の多数実績と高いノウハウを活かした製品です。
材質 | SUS材 |
サイズ | |
開発期間・納期目安 | - |
交差レベル | - |
製品用途 | 発電プラント |
TIG溶接とは?~まとめ~
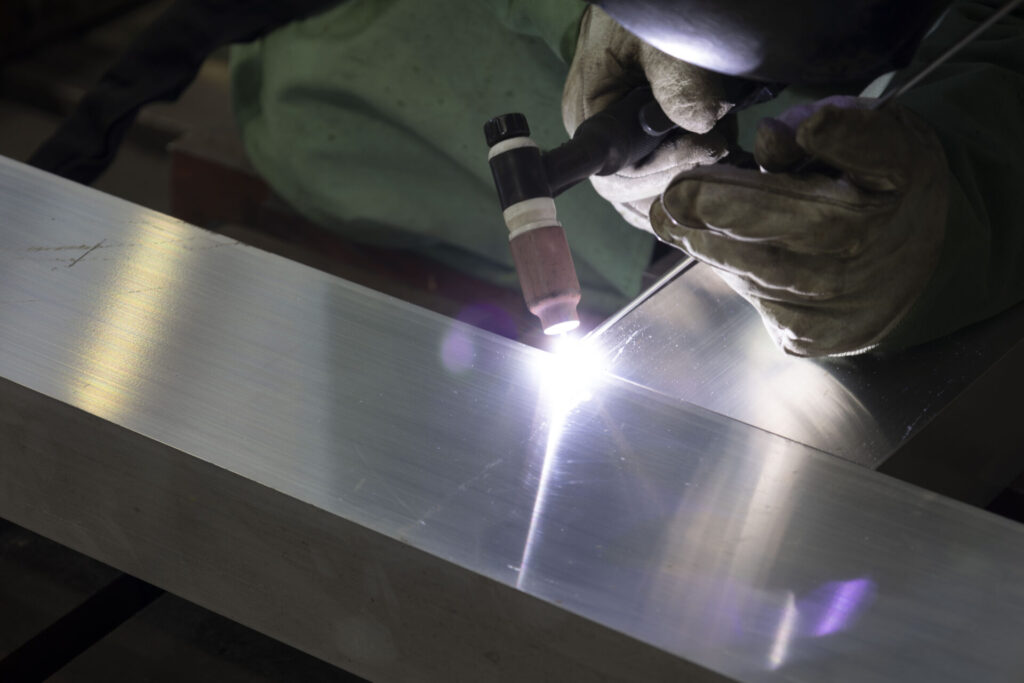
溶接技術は、製造業の発展において欠かせない重要な技術です。特にTIG溶接は、高精度かつ高品質な溶接を可能にする方法であり、鉄鋼やステンレス鋼だけでなく、アルミニウムやマグネシウムといった熱伝導率の高い金属の溶接にも適しています。アルミ溶接においては、熱歪みや酸化被膜の問題などがあるため、高度な技術とノウハウが求められます。
アルミ溶接は、非常に高い技術力と専門知識を要する分野です。その理由は、アルミニウムの熱伝導率が高く、熱歪みや酸化被膜の形成が起こりやすいため、溶接品質に大きな影響を与えるからです。当社ではこれまでに培ったノウハウと高品質な溶接技術を基に、TIG溶接の特性を活かし、熱制御技術を駆使することで、安定した品質と優れた仕上がりを実現できます。高度なアルミ溶接技術が必要な際は、ぜひ当社までご相談ください。
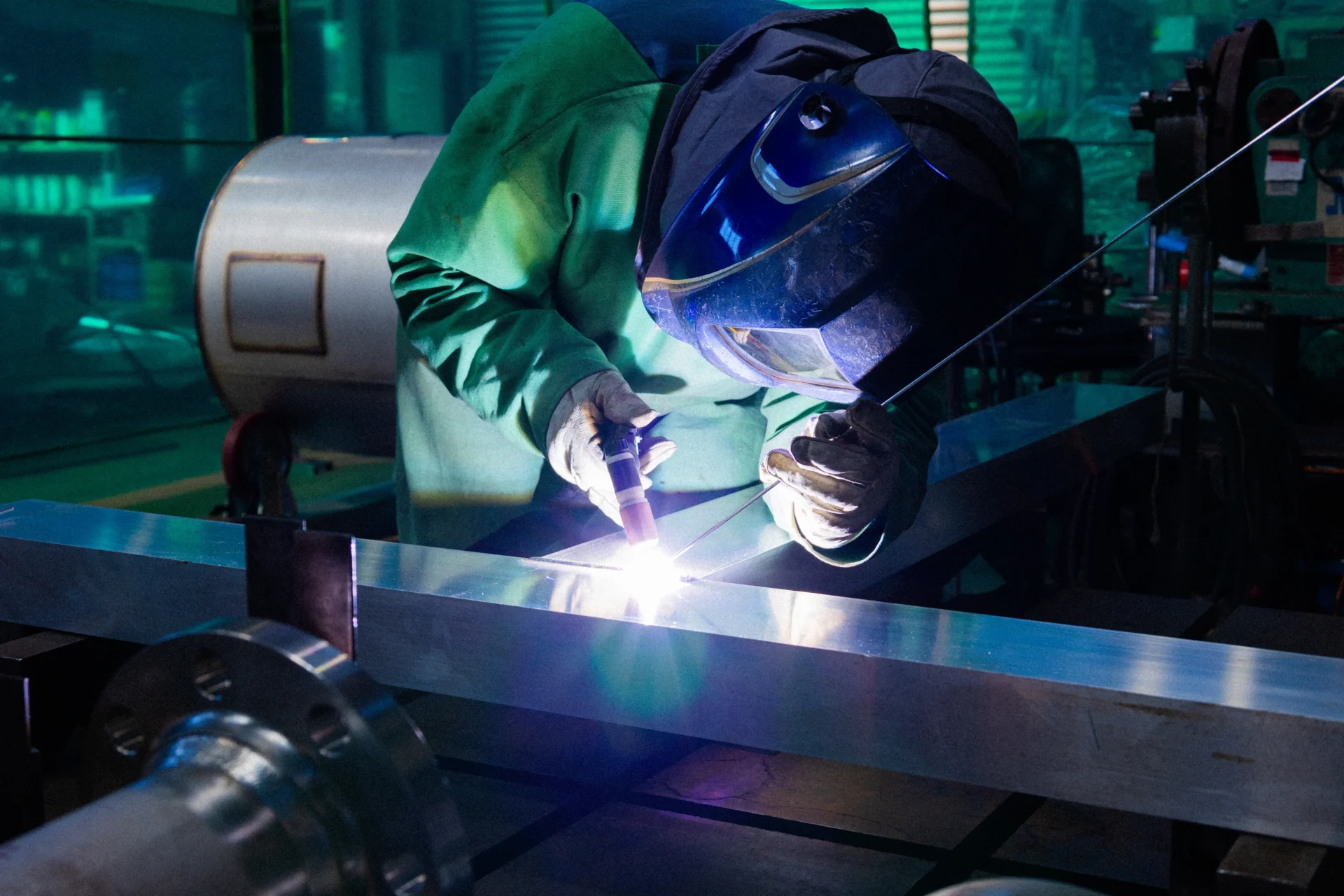
お問い合わせ
ご相談・お見積り依頼などお気軽にお問い合わせください